Minimizing Production Loss – The Importance of Effective Machine Downtime Tracking
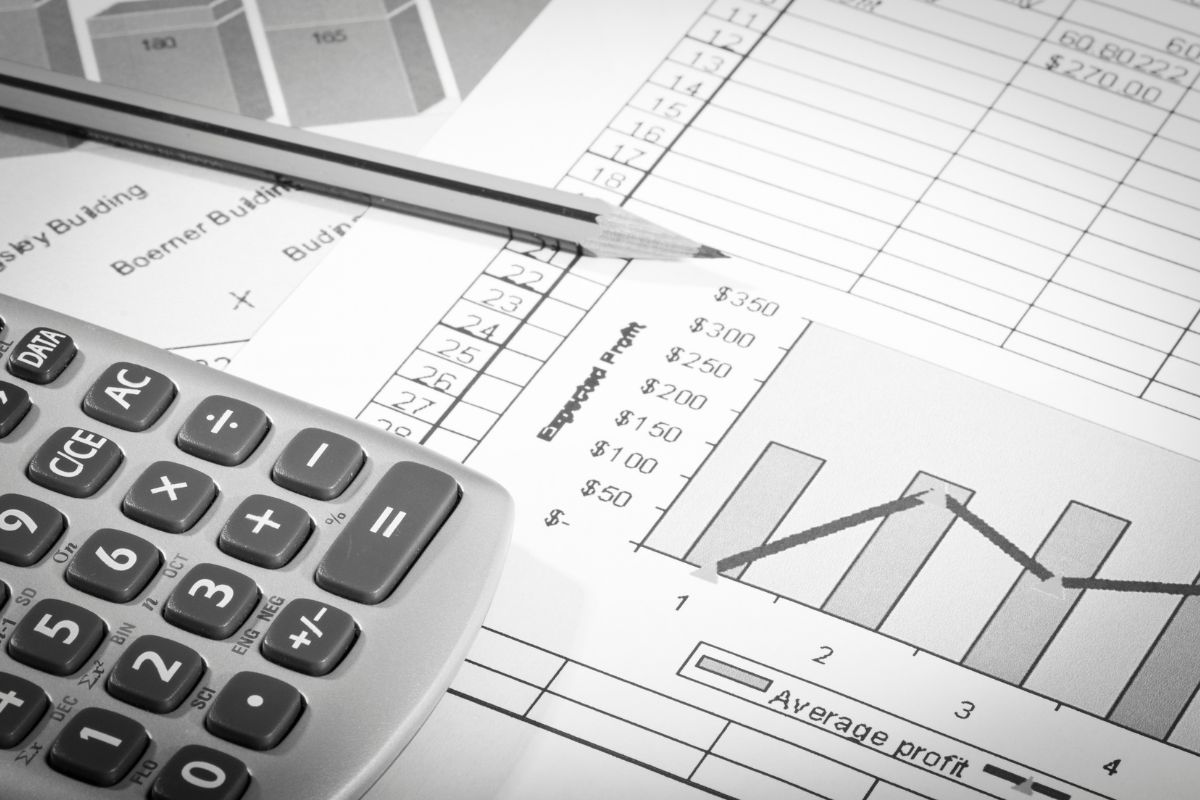
Machines that run continuously will eventually break down. This can result in costly downtime, which has the potential to impact both production and the bottom line. It’s important to know what Machine downtime is and how it can be tracked effectively so that you can manage it better and be more efficient with your time.
Table of Contents
Downtime is a term used to describe the time when a machine is not producing. Downtime can be caused by many factors, including equipment breakdown and maintenance. It can also result from operator error or weather conditions such as rain or snow that prevent you from moving heavy equipment around your facility. Additionally, environmental factors like humidity or extreme temperatures may cause issues with your equipment’s performance and increase downtime rates for certain types of machines (such as those used in manufacturing).
To calculate machine downtime, you need to know the following:
When it comes to calculate machine downtime, the responsibility doesn’t fall on just one person. As with most tasks in manufacturing, it’s a team effort that requires collaboration between all parties involved. To minimize production losses and improve efficiency, everyone should have a clear understanding of their role and how they can contribute to the overall goal of minimizing machine downtime.
The best way for this kind of teamwork to happen is through regular meetings where relevant information is shared among all members of your team–including operators, maintenance personnel and even management staff if needed. These meetings should take place regularly (ideally weekly) so that progress can be discussed openly without having too much time pass between discussions about current issues or new ideas for improvement plans for next week’s meeting agenda items will include things like:
You may be surprised to learn that the cost of machine downtime is much more than you think. If your company produces products or provides services, then it’s likely that your business relies on many machines to make things happen. Every day these machines are running, they’re producing something valuable for you and your customers–whether it’s widgets web pages or customer service calls.
But what happens when one or more of those machines breaks down? How much does this affect production levels? What kind of impact does it have on customer satisfaction? And most importantly: how much money do you lose as a result?
If you don’t know how much time is being lost because of broken equipment, then there’s no way for anyone at any level within an organization (from executive management down through supervisors) to understand exactly how much money could be saved by preventing downtime incidents from happening again in future months/years…or even days!
Tracking machine downtime is an important part of maintaining your facility. However, it can be difficult to keep track of all the different factors that contribute to downtime. Automated machine downtime tracking solutions like LineView can help you identify problems and make improvements by providing a detailed breakdown of the costs associated with machine downtime.
In addition, these tools allow you to see trends in how much money is being spent on fixing machines that are down, as well as how often they go down. This information will help you prioritize which parts need maintenance or replacement so that you’re spending less time dealing with broken equipment and more time focusing on other aspects of running your business
The first step in reducing errors in machine downtime tracking is to make sure that all downtime is recorded. If a machine breaks down, you need to know about it–and then you can decide what the next steps are going to be.
You should also review the data regularly so that you can make sure that it’s accurate and up-to-date. If a machine has been down for several weeks, but hasn’t been recorded as being out of service during those weeks because someone forgot or didn’t think it was important enough (or maybe they just didn’t have time), then there could be a big problem when you try to get back up again after this extended period without productivity!
Finally: use an easy-to-use machine downtime tracking system! This will save everyone involved from having too much work on their hands when something goes wrong with one part of the process; instead, they’ll just have one place where they can go look up all relevant information regarding what went wrong before moving forward again without missing any steps along the way.”
Effective machine downtime tracking can lead to significant cost savings and a better bottom line.
By tracking machine downtime and using the data to identify areas of improvement, you can reduce your production loss and improve your bottom line. This is an important part of any manufacturing business, but it’s especially important if you’re tracking machines individually rather than as part of a larger production line or facility.
Sign up to receive our email, delivering the latest stories straight to your inbox.